Selection and techniques for overlay welding
Overlay welding is a versatile welding process applied to enhance the surface properties of components, such as wear resistance, corrosion resistance, or heat resistance. The choice of overlay welding techniques depends on several key criteria:
1.Meeting the performance requirements of the overlay
2.Suitability for the structure of the workpiece
3.Compatibility with metallurgical characteristics
4.Appropriate use of overlay welding materials
5.Efficiency and cost-effectiveness
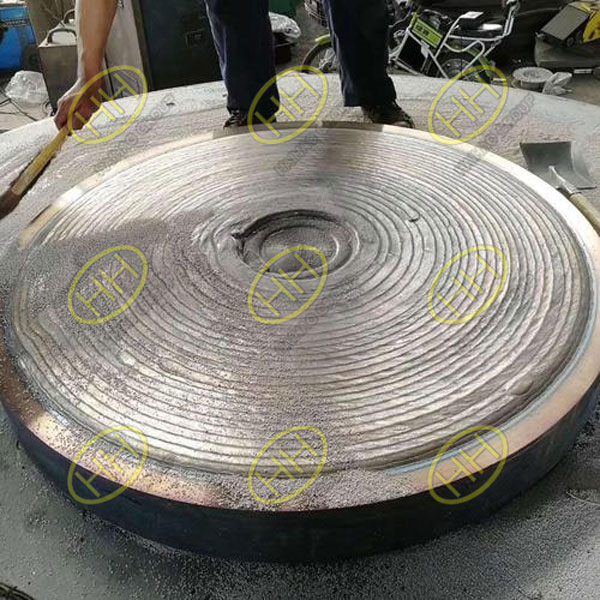
Flange with inconel 625 cladding
Below is an overview of common overlay welding techniques and their specific applications.
1.Oxy-Acetylene Overlay Welding
This method is ideal for precision and small-scale overlay welding, producing smooth and clean overlays. Common applications include components such as valves, band saws, and plowshares.
2.Shielded Metal Arc Overlay Welding
Suitable for small-scale production and repair of worn components, this method offers versatility and simplicity, making it a go-to choice for batch work.
3.Submerged Arc Overlay Welding
Best suited for large-scale, horizontal overlay welding tasks, this technique is widely used for applications like container walls and rolls. Its high deposition efficiency makes it a cost-effective option for large areas.
4.Gas Metal Arc Overlay Welding
Argon Protection: Used for cobalt, nickel, aluminum-based alloys, and bronze. This technique is common in precision applications where non-ferrous alloys are required.
CO₂ Protection: Ideal for ferrous alloys, including applications like bearing shells and mud pumps.
5.Gas Tungsten Arc Overlay Welding
This method is used for complex, high-precision small parts, such as turbine blades, which often require cobalt-based overlays. It is also effective for aluminum and nickel-based alloys.
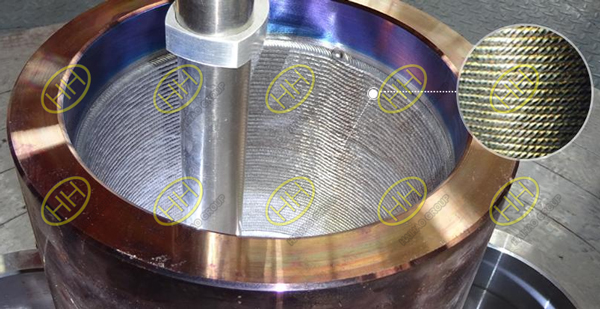
Overlay Welding Process
6.Plasma Arc Overlay Welding
A highly versatile process capable of overlay welding iron-based, nickel-based, cobalt-based, and refractory metals. Common applications include flow control valves, extruder screws, and automotive engine exhaust valves. Its ability to handle intricate geometries makes it highly effective for advanced applications.
7.Electroslag Overlay Welding
Designed for thick materials and inclined surfaces (45–60°), this method also supports horizontal and vertical overlay welding when molds are used. It is commonly applied to large, heavy components.
Choosing the appropriate overlay welding technique depends on the performance requirements, material characteristics, and economic considerations of the task. From small precision parts to large-scale industrial components, these processes ensure that overlay welding can address a wide range of operational demands, improving the durability and efficiency of components across industries.