Preheating and post-weld cooling in overlay welding
Preheating and controlled post-weld cooling are essential techniques in overlay welding, especially when working with carbon steel and low-alloy steel prone to cracking and spalling. These measures help improve welding quality and durability.
Preheating Before Welding
The primary purpose of preheating is to reduce the risk of cracking. The required preheating temperature depends on factors such as the carbon equivalent (Ceq) of the overlay metal, the material of the workpiece, its size, and the rigidity of the weld area. Typical preheating temperatures range from 150°C to 600°C.
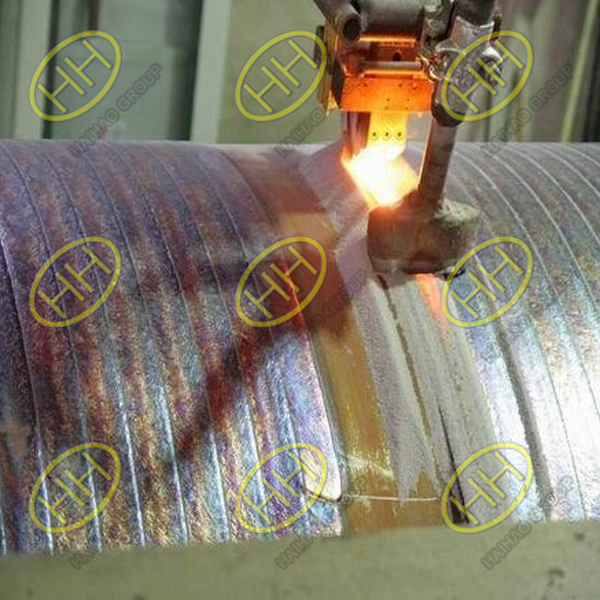
Preheating in overlay welding
Preheating guidelines based on carbon equivalent values:
Ceq ≤ 0.4%: Preheat above 100°C
Ceq ≤ 0.5%: Preheat above 150°C
Ceq ≤ 0.6%: Preheat above 200°C
Ceq ≤ 0.7%: Preheat above 250°C
Ceq ≤ 0.8%: Preheat above 300°C
For workpieces with high hardness overlays or large surface areas—such as forging molds or large valve bodies—overall preheating is recommended. For localized overlay welding, localized preheating can be sufficient. Small components that are uniformly heated during the welding process may not require preheating.
Post-Weld Cooling
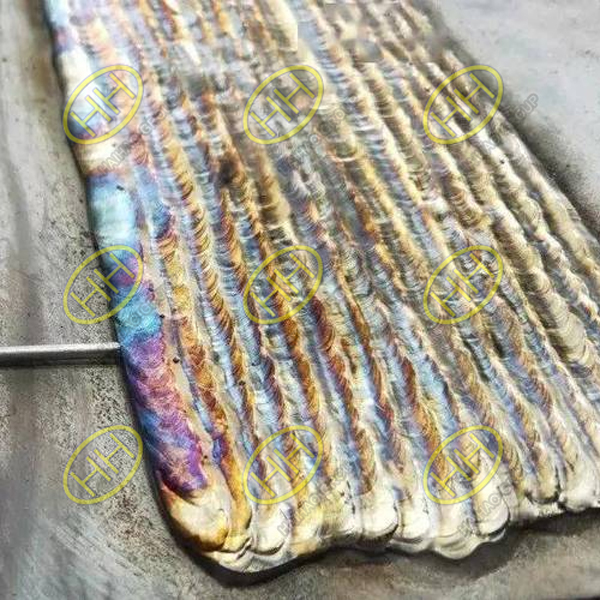
Post Weld Cooling in Overlay Welding
To further prevent cracking and spalling, controlled cooling after welding is crucial. Post-weld cooling methods include:
1.Slow Cooling:
Place the welded component in insulating materials such as asbestos ash, asbestos blankets, or aluminum silicate to ensure gradual cooling. This method minimizes residual stress and prevents cracking.
2.Air Cooling:
For metals with low hardening tendencies (e.g., 1Cr13, 2Cr13), air cooling can be used to achieve higher hardness. These components often require no additional heat treatment after mechanical processing.
3.Tempering and Slow Cooling:
For metals with high hardening tendencies (e.g., high-chromium cast iron, tungsten carbide, cobalt-based alloys), post-weld heat treatment is critical. This involves tempering at 600–700°C for one hour, followed by slow cooling to relieve stress and prevent cracking.
By adopting proper preheating and post-weld cooling techniques, overlay welding can achieve higher quality and reliability. These measures are essential for applications involving high-hardness overlays, large workpieces, or materials prone to cracking. Proper thermal management during welding ensures the structural integrity and long-term performance of the welded components.