Installation guidelines for orifice flanges and internal weld seam grinding
Orifice flanges are critical components in flow measurement systems. They are commonly used in conjunction with orifice plates to accurately monitor fluid flow in industrial pipelines. Proper installation and weld treatment of orifice flanges are essential to ensure measurement accuracy, system integrity, and long-term performance. This article outlines the key precautions and best practices for the installation of orifice flanges and the grinding of internal weld seams.
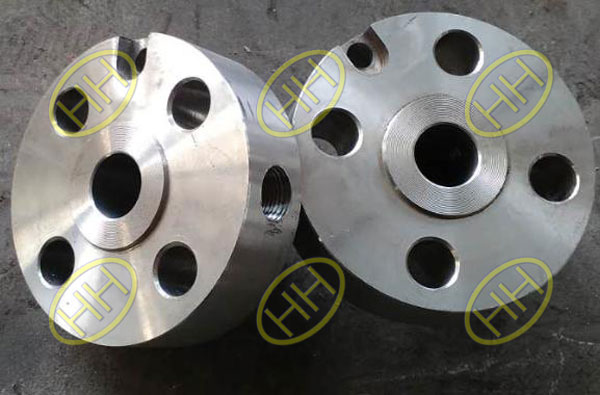
ASTM A182 F304 Weldind Neck Orifice Flange Finished In Haihao Flange Factory
1.Weld-Free Zones for Accurate Flow Measurement
To maintain the accuracy of the differential pressure readings across the orifice plate:
Ensure no welds (except for the flange welds themselves) are present in a straight pipe section that is:
10 times the pipe outer diameter (OD) upstream of the orifice plate
5 times the pipe OD downstream of the orifice plate
These weld-free zones are critical to minimize turbulence and ensure a stable flow profile, which directly affects the precision of the flow readings.
2.Impulse Line Orientation
The orientation of impulse (pressure tapping) lines must follow the direction indicated in the isometric drawing. In general:
For gas services, pressure tapping lines should face upward
For liquid services, they should face downward, or within ±45 degrees from the vertical axis (either up or down)
Correct orientation ensures accurate pressure transmission, prevents gas or liquid entrapment in the impulse line, and facilitates proper drainage or venting.
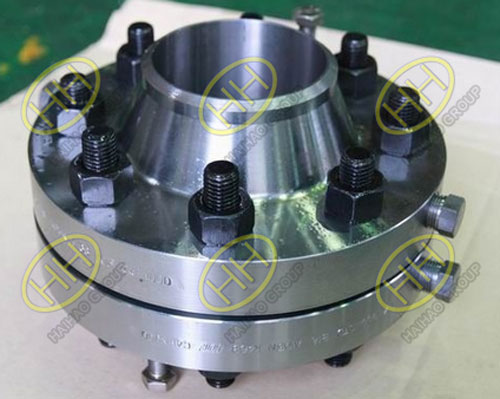
Orifice Flange
3.Internal Weld Seam Grinding
After welding the orifice flange to the pipe, internal weld seam grinding must be performed to eliminate any irregularities inside the pipe that could disturb flow:
Smooth and flush finish: Grind the internal weld seam until the inner surface is flush and free from protrusions or irregular weld beads.
No steps or ridges should remain that may affect fluid flow or create turbulence.
This operation is essential to maintain a uniform inner diameter, ensuring that the orifice plate reads accurately without being influenced by weld irregularities or flow disruptions.
4.Quality Acceptance Criteria
The grinding process is considered acceptable when:
The internal weld seam is level with the inner pipe surface
There are no sharp edges, burrs, or protrusions
The transition between the pipe and flange is smooth and continuous
Proper finish reduces flow disturbance and extends the service life of both the flange and measuring equipment.
The precise installation of orifice flanges and proper treatment of internal weld seams are crucial for maintaining accurate flow measurement in process piping systems. By following these guidelines:
- Measurement errors can be minimized
- System reliability and safety are enhanced
- Maintenance and inspection become more efficient
At Haihao Group, we understand the importance of these details. That’s why we deliver not only certified flange products but also technical guidance to help our clients implement industry best practices. Email:sales@haihaogroup.com