How to ensure quality in duplex stainless steel spectacle blind flanges?
Duplex stainless steel ASTM A240 UNS S31803 is widely used in critical applications requiring high strength and excellent corrosion resistance. However, to guarantee the performance of spectacle blind flanges, stringent quality control measures are essential. In this article, we will explore key quality indicators and testing methods to ensure the reliability of duplex stainless steel flanges.
Key Quality Indicators for S31803 Spectacle Blind Flanges
To meet international standards and withstand harsh environments, S31803 duplex stainless steel spectacle blinds must pass multiple quality assessments, including:
Pitting Resistance Equivalent Number (PREN ≥ 35) – Ensures excellent resistance to pitting and crevice corrosion, especially in chloride-rich environments like offshore and chemical industries.
Ferrite Content (30-55%) – Maintaining the correct balance of ferrite and austenite ensures optimal mechanical properties and corrosion resistance.
Hardness Testing (≤ 290 HBW) – Prevents material embrittlement and ensures durability under stress.
Pitting Corrosion Testing – Confirms resistance to localized corrosion, particularly in aggressive media.
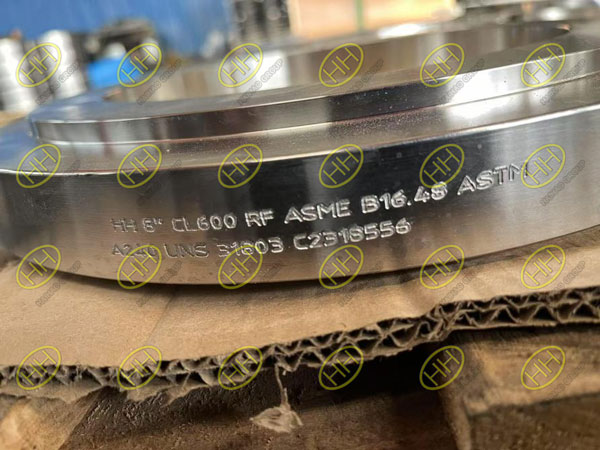
Duplex stainless steel ASTM A240 UNS S31803 Spectacle Blind Flange
Non-Destructive Testing (NDT): Ensuring Flange Integrity
Non-destructive testing (NDT) is crucial for detecting internal and surface defects without compromising the product’s integrity. The most common NDT methods for duplex stainless steel spectacle blind flanges include:
Ultrasonic Testing (UT) – Detects internal flaws such as inclusions or cracks that could weaken the flange.
Radiographic Testing (RT) – Provides an in-depth analysis of internal structures, ensuring uniformity.
Magnetic Particle Testing (MT) – Identifies surface and near-surface defects in ferritic materials.
Dye Penetrant Testing (PT) – Helps reveal surface cracks or imperfections that might not be visible to the naked eye.
Low-Temperature Impact Testing (-46℃, Minimum 35J): Why It Matters?
In cryogenic applications such as LNG pipelines and offshore platforms, low-temperature impact resistance is critical. Charpy V-notch impact testing is conducted at -46°C to ensure the material maintains toughness under extreme conditions.
Minimum absorbed energy: 35J – Prevents brittle fracture in cold environments.
Ensures safety and reliability – Reduces the risk of sudden failure in low-temperature applications.
Meets stry standards – Required for compliance with ASME, ASTM, and EN 10204-3.1 certifications.
Haihao Group’s Quality Control Process
At Haihao Group, we follow a comprehensive quality assurance program to guarantee that every S31803 spectacle blind flange meets or exceeds industry standards:
Positive Material Identification (PMI) Testing – Verifies chemical composition to ensure correct alloy grade.
Dimensional Inspection – Uses precision measuring tools to confirm compliance with ASME B16.48.
Hardness Testing – Ensures the material remains within the acceptable hardness range for durability.
Microstructure Analysis – Examines ferrite-austenite balance to maintain mechanical strength.
Full Documentation & Certification – Provides EN 10204-3.1 certificates with detailed test results for complete traceability.
To ensure the highest quality in duplex stainless steel spectacle blind flanges, rigorous testing and inspection processes are necessary. From PREN verification to low-temperature impact tests, each step plays a crucial role in guaranteeing performance and durability.
At Haihao Group, we are committed to delivering high-quality, internationally certified duplex stainless steel flanges to meet the demands of industries such as oil & gas, chemical processing, and LNG.
Contact us today to learn more about our S31803 duplex stainless steel solutions! Email:sales@haihaogroup.com