Ensuring excellence with ultrasonic testing for ASME B16.5 flanges ordered by UAE client
At Haihao Group, we are committed to providing our clients with the highest quality piping components, meeting the most stringent industry standards. Recently, our esteemed client in the UAE placed an order for ASME B16.5 flanges, and we have ensured that these flanges undergo comprehensive ultrasonic testing (UT) to guarantee their quality and reliability. Ultrasonic testing is a critical non-destructive testing method that helps us detect internal flaws and ensure the structural integrity of our products.
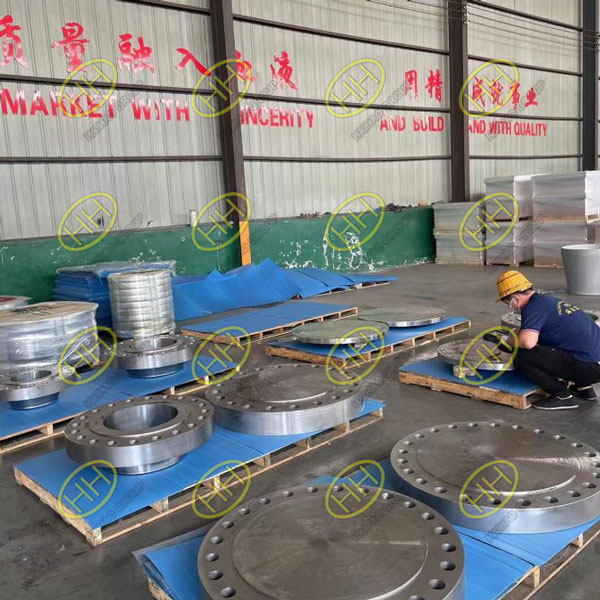
Ultrasonic Testing for ASME B16.5 Flanges
The Ultrasonic Testing Process
Preparation
Cleaning: The flange surfaces are thoroughly cleaned to remove any contaminants such as dirt, oil, or rust that might interfere with the ultrasonic waves.
Selection of Probe: Depending on the material and thickness of the flange, a suitable ultrasonic probe (transducer) is selected. The probe type (angle, frequency) is crucial for accurate detection.
Calibration
Reference Standards: The ultrasonic testing equipment is calibrated using reference standards with known dimensions and defect characteristics. This ensures the accuracy and reliability of the test results.
Adjustment: The instrument settings are adjusted to match the material properties and the expected flaw types. This includes setting the appropriate gain, range, and other parameters.
Scanning
Couplant Application: A couplant (usually a gel or oil) is applied to the flange surface to facilitate the transmission of ultrasonic waves from the probe into the material.
Probe Movement: The ultrasonic probe is moved over the surface of the flange in a systematic pattern to ensure complete coverage. This can be done manually or using automated scanners for large or complex components.
Detection
Wave Transmission: The ultrasonic waves are transmitted into the flange material. When these waves encounter a discontinuity (such as a crack or inclusion), they are reflected back to the probe.
Signal Interpretation: The reflected signals are displayed on the ultrasonic testing device’s screen, where they are analyzed by trained technicians. The amplitude and time-of-flight of the signals provide information about the size, location, and nature of any detected flaws.
Evaluation
Flaw Assessment: Detected flaws are assessed against predefined acceptance criteria based on industry standards and client specifications. This determines whether the flange meets the required quality levels.
Documentation: Detailed records of the testing process, including equipment settings, calibration details, scan results, and flaw evaluations, are documented for traceability and quality assurance.
Reporting
Test Report: A comprehensive test report is generated, summarizing the findings of the ultrasonic testing. This report includes descriptions of any detected flaws, their locations, and the overall assessment of the flange’s integrity.
Client Communication: The test report is shared with the client, providing transparency and assurance of the product’s quality.
Haihao Group’s dedication to quality and reliability is reflected in our rigorous testing procedures. By conducting thorough ultrasonic testing on the ASME B16.5 flanges ordered by our UAE client, we ensure that every product meets the highest standards of structural integrity and performance. Our commitment to excellence and adherence to industry standards guarantee that our clients receive products they can trust for their critical applications. For more information about our products and services, please visit our website or contact our sales team.